“Fishbowl was holding us back. We couldn’t trust the numbers, and every little task took forever. Elevated Signals changed everything. Now, we can track batches, update work orders in real-time, and fix mistakes easily. It’s not just easier—it’s giving us the confidence to move into nutraceuticals and get GMP-certified.” - Perry Bowman, Quality Lead at Honest PP&D
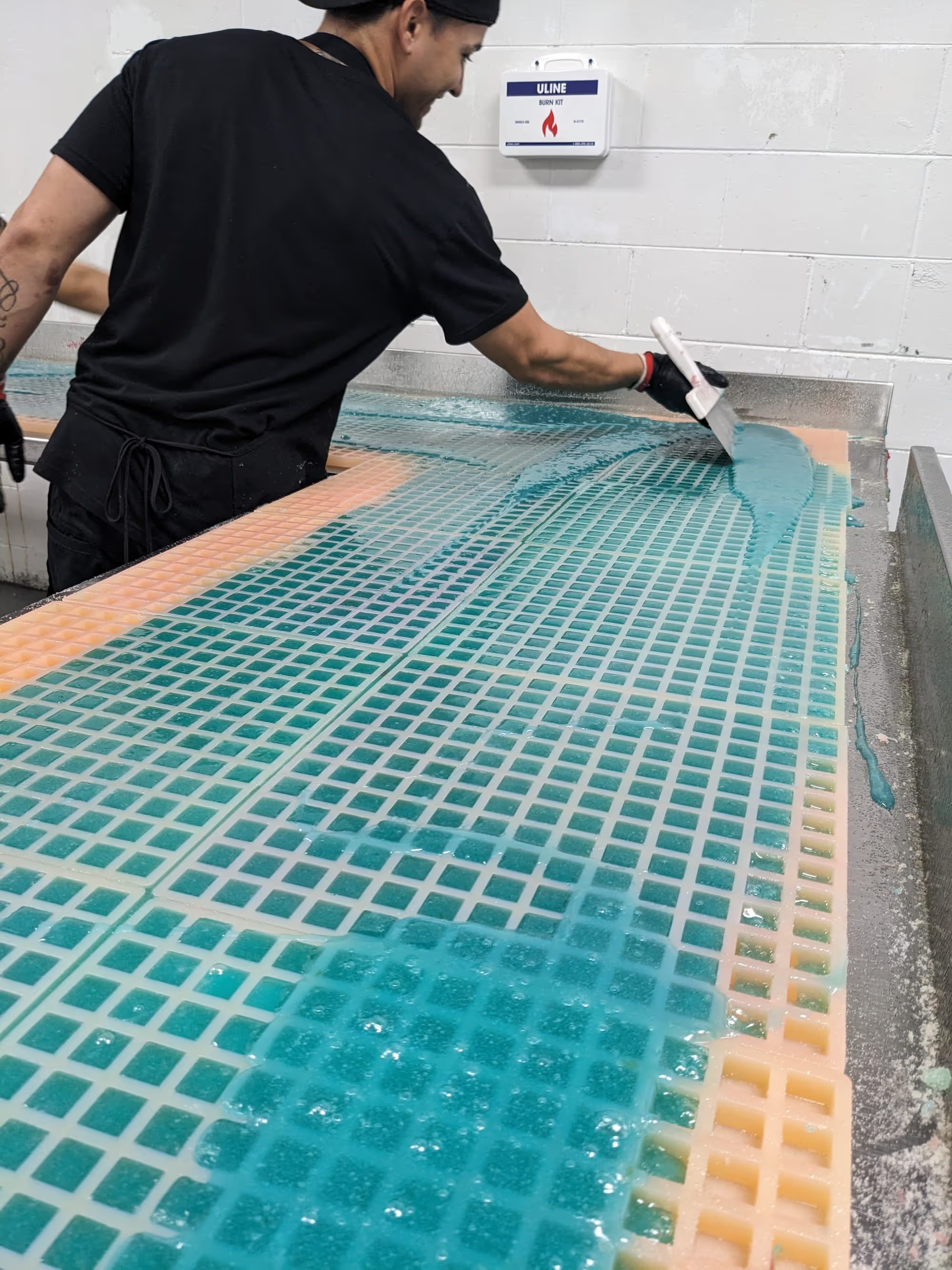
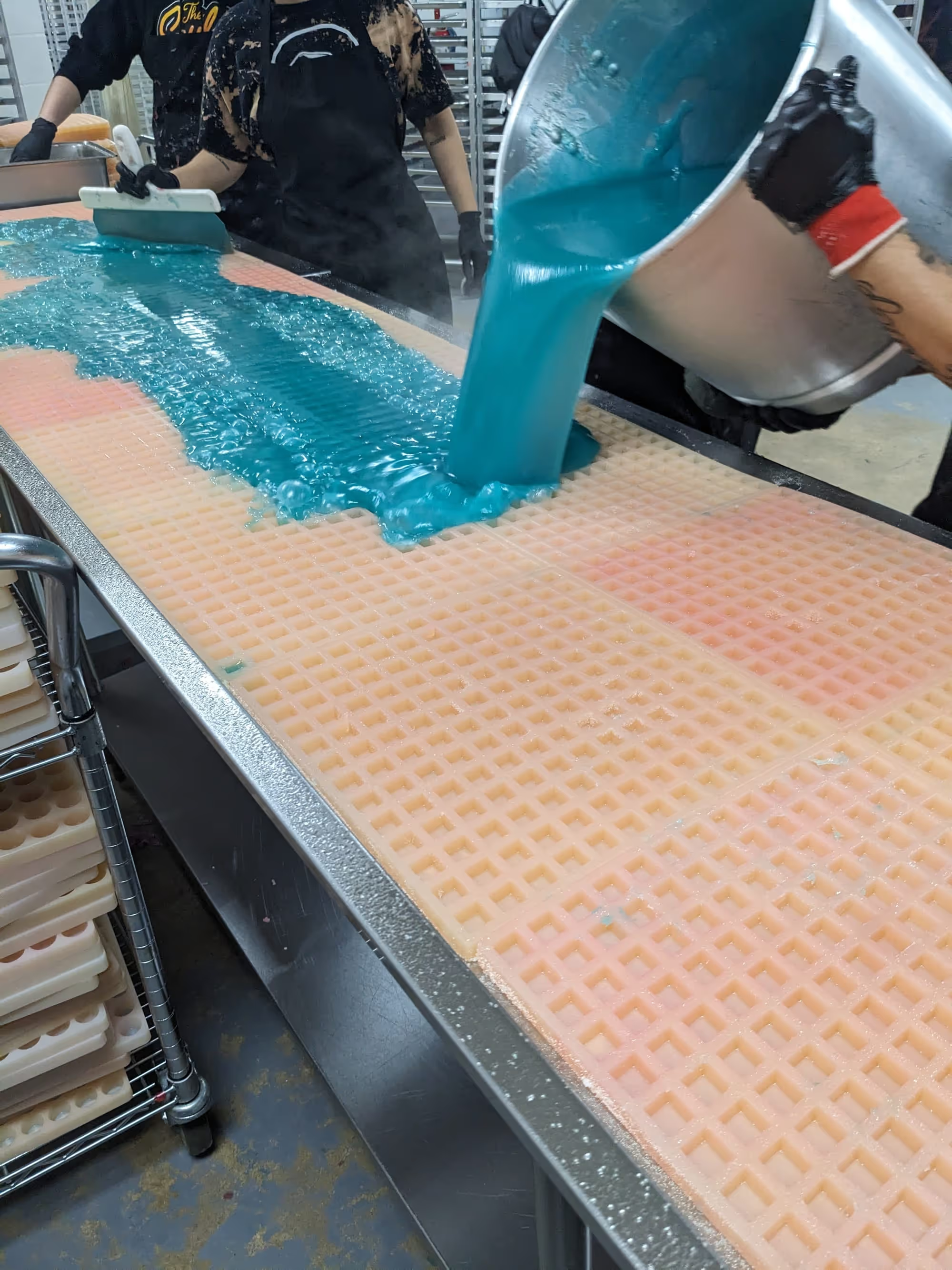
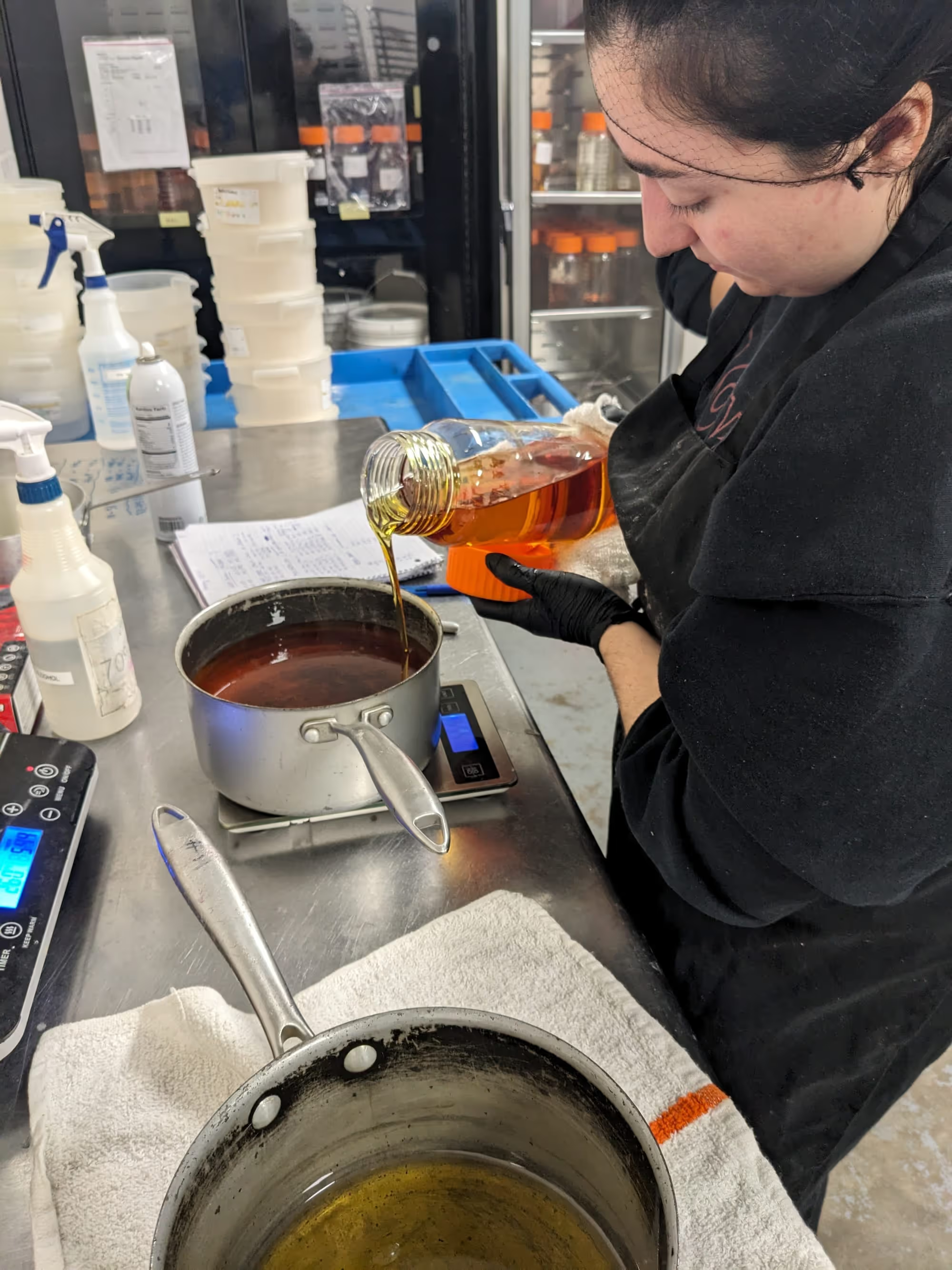
About Honest PP&D
Honest PP&D started as a small co-packer, producing hemp-based products like gummies, chocolates, and vapes. Business was booming, and production quickly expanded to produce over 700 unique products in their Florida facility.
But with rapid growth came new challenges: disorganized inventory, time-consuming processes, and mounting compliance pressures.
Honest PP&D’s tools - Fishbowl software and spreadsheets - weren’t keeping up with the complexities of a growing manufacturing operation. Inventory numbers were unreliable, workflows were time-consuming, and staying audit-ready felt like an uphill battle. The final straw came during an unplanned audit, where gaps in its processes became impossible to ignore. The team knew they needed a better solution to sustain growth.
That’s when Honest PP&D found Elevated Signals, a manufacturing software that simplified their workflows and gave the team full control over inventory and compliance. As a result, they had the confidence to pursue a GMP certification and enter a new market - nutraceuticals.
The Situation 👇
Honest PP&D’s Growth Journey and Challenges
As Honest PP&D scaled its manufacturing operations, its inventory software began to cause frustration across the team:
- Unreliable inventory: The inventory in the software rarely matched what was on the shelf. Production was delayed when key ingredients weren’t available, even though the system said they were.
- Lack of traceability: The team couldn’t connect raw materials to finished goods, which made it difficult to manage quality and left them scrambling during audits.
- Frustrating workflows: Updating work orders required starting from scratch. Small changes, like adjusting a recipe, meant wasting time recreating documents slowing down production with daunting admin work.
- No support when it mattered: When the team reached out for help from their software provider, responses were slow and unhelpful. Without proper training, they were left to figure things out on their own, leaving issues unresolved and the team frustrated.
- Clunky QuickBooks integration: While Fishbowl claimed integration with QuickBooks, syncing data could take up to a full day. This lag made the integration nearly useless for real-time decision-making and added delays to their workflow.
- Manual and Outdated Setup: Fishbowl’s server-based system required manual software installation on every device. Essential features like purchase orders had to be purchased separately, adding extra steps and costs. Even worse, the system frequently failed to open on Apple devices, leaving employees stuck and frustrated.
“Fishbowl made everything harder, we couldn’t trust the data, and every little task felt like a huge challenge. It just wasn’t built for how we work.” - Perry Bowman, Quality Lead at Honest PP&D
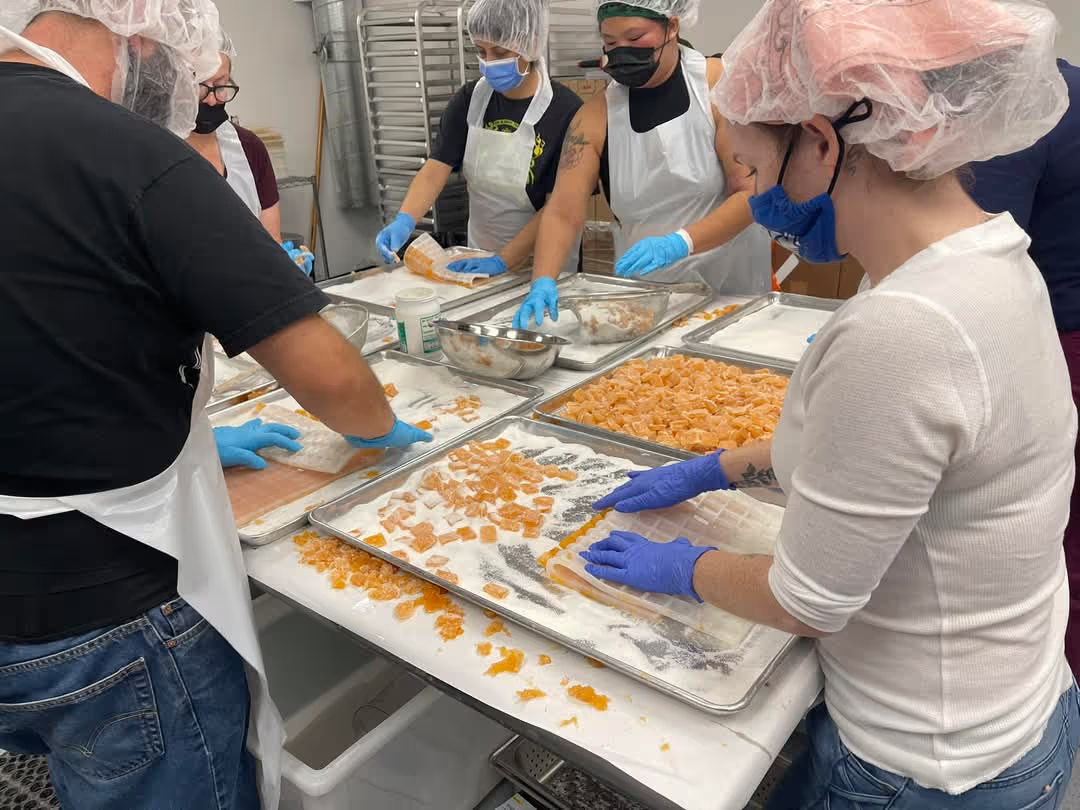
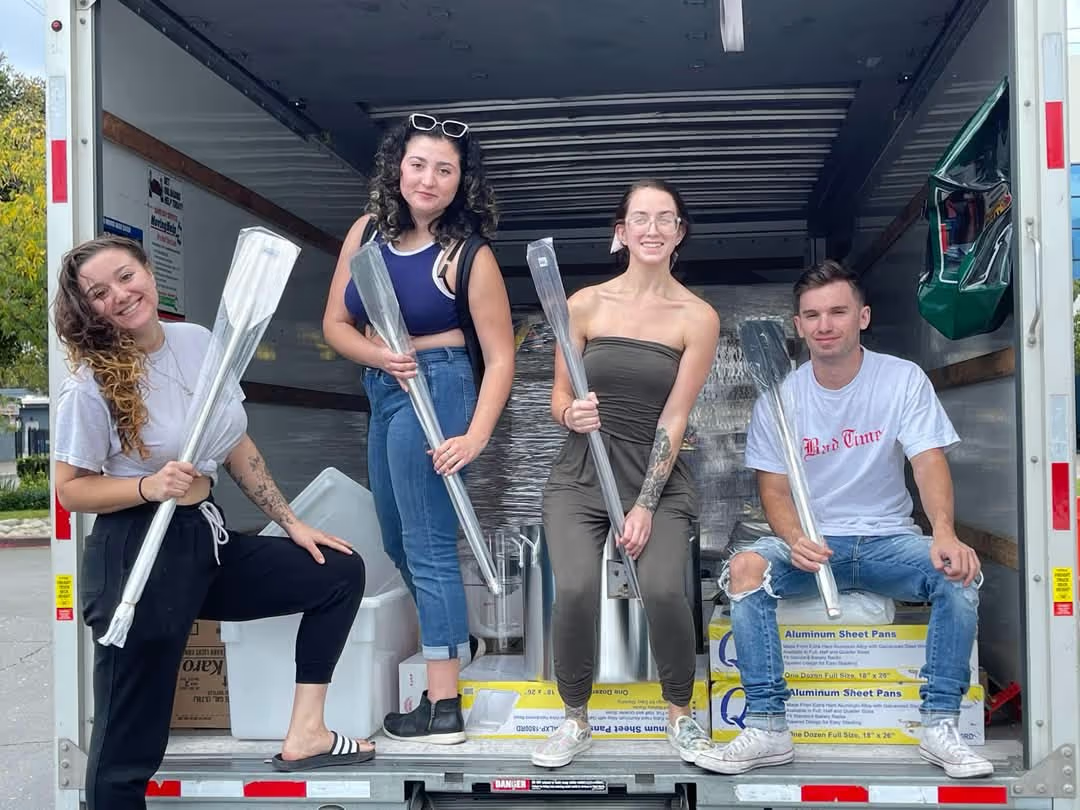
The Solution 👇
Honest PP&D’s Transformation with Elevated Signals
Honest PP&D partnered with Elevated Signals to address operational challenges and set the foundation for future growth. The software’s intuitive design, robust tracking features, and hands-on support transformed how the team worked.
How Elevated Signals Helps:
1. Trustworthy, real-time data
Elevated Signals provides Honest PP&D with real-time tracking of raw materials, work-in-progress, and finished goods. This accuracy means no more production delays caused by missing inventory.
2. Traceability and audits made easy
Elevated Signals’ batch tracking connected raw materials to finished goods, giving Honest PP&D full visibility of their operations. The team now feels prepared for audits and can quickly pinpoint and resolve quality issues.
3. Workflows without the frustration
Work orders are no longer a headache. Elevated Signals makes updates to processes quick and simple, with auto-save and real-time adjustments that keep production running smoothly.
4. Support that has your back
From day one, the Elevated Signals team provided tailored training and ongoing guidance. Honest PP&D gained the confidence to adopt the system and get the most out of its features—something they had never experienced with their previous system.
5. Built for compliance and growth
With improved data transparency, traceability, and regulatory readiness, Honest PP&D feels equipped to pursue a GMP certification. Elevated Signals gives them the confidence to take the next step toward entering the nutraceutical market.
“After that first call, I knew this was the solution we needed, Elevated Signals wasn’t just another software—it solved the exact problems we were stuck on and gave us a way forward.” - Perry Bowman
The Impact 👇
What Changed for Honest PP&D?
Switching to Elevated Signals didn’t just solve Honest PP&D’s problems—it gave the team complete visibility into inventory and traceability as well as the confidence to break into new markets:
- 30–40 minutes saved per production run: Automating work orders and eliminating manual QA paperwork saves the team time, allowing them to focus on new products and speeding up production.
- Traceability that works: Batch tracking lets them trace raw materials to finished goods, making it easy to catch and fix issues before they spiral into bigger problems.
- Fewer costly mistakes: Real-time data and streamlined workflows have drastically reduced errors that once disrupted operations and wasted resources.
- Audit readiness: Comprehensive batch tracking made it easy to stay compliant, reducing the stress and time involved in audits.
- A clear path to GMP certification: Honest PP&D now has the tools and confidence to meet industry standards and enter the nutraceutical market.
Are you looking for software to help you manage your production inventory? Learn how Elevated Signals’ manufacturing software can help .